20 Minutes to 5: Luna Grill's Cooling Efficiency Success with ConnectedFresh
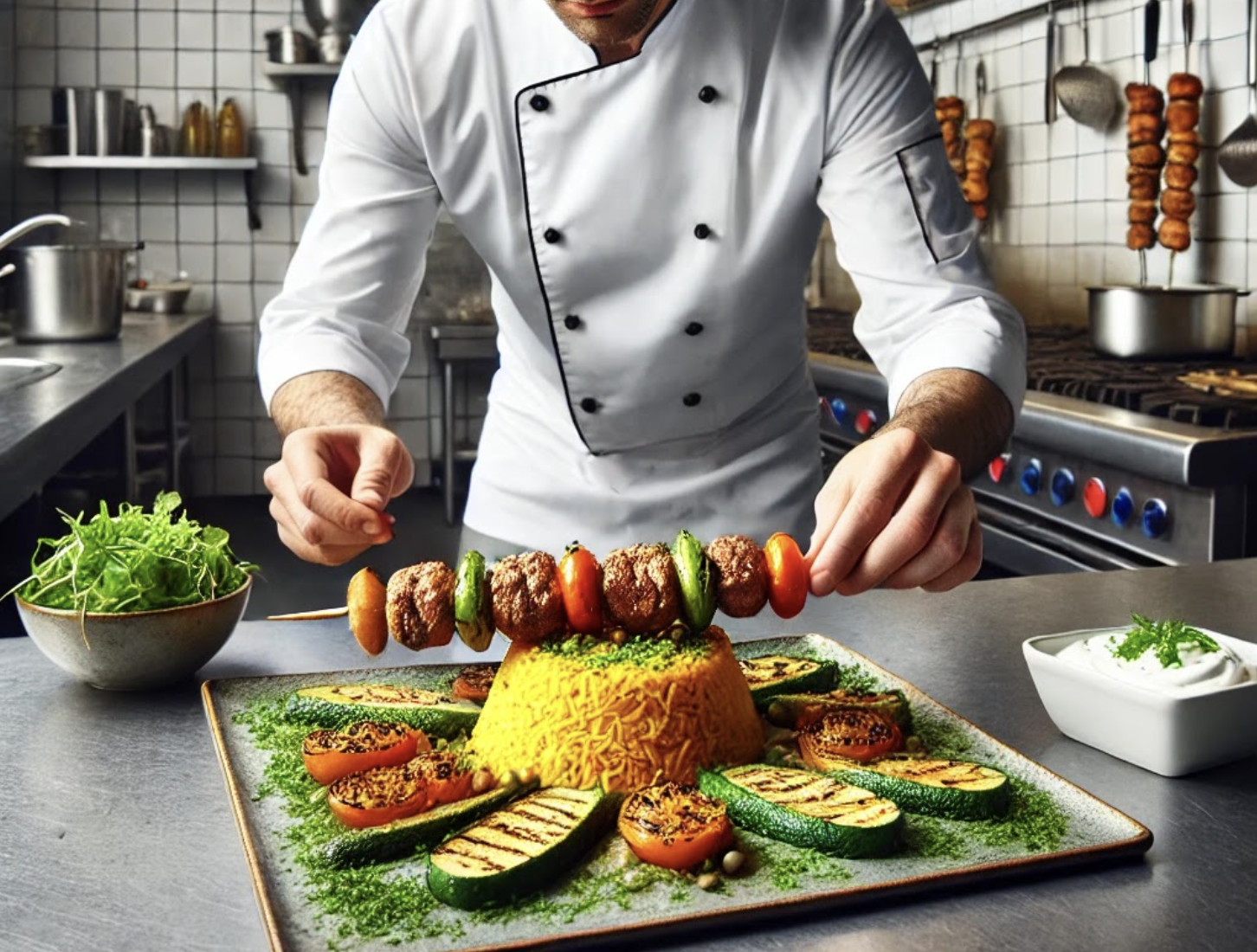
Impact Overview
- Thousands of Labor Hours Saved: Reduction in manual processes allowed the team to reallocate their time to customer-oriented tasks.
- Enhanced Food Safety Compliance: Automated alerts and detailed logging ensured the highest standards in health compliance, providing both efficiency and peace of mind.
- Significant Time Reduction in Cooling Logs: Reduced from 20 minutes to less than 5 minutes - a 75% reduction, improving productivity across all locations.
- Daily Automated Reports: Store managers and Luna Grill leadership receive detailed automated reports daily, ensuring ongoing compliance and awareness of cooling processes.
ConnectedFresh took the manual labor and potential for human error out of the process. What used to take an average of 20 minutes per cooled ingredient now takes less than 5 minutes, saving us thousands of hours across our restaurants. - Maddie Ahrens, Director of Culinary & Restaurant Excellence at Luna Grill
Luna Grill: Elevating Mediterranean Freshness with IoT Insights
Luna Grill, a rapidly growing Mediterranean fast-casual chain, prides itself on delivering fresh, quality ingredients to its guests. With more than 50 locations spread across Southern California, Texas, and beyond, Luna Grill faced the challenge of ensuring consistent food quality and safety while expanding its operations. Enter ConnectedFresh: a solution that not only brought automation to their food safety processes but also empowered their teams with real-time insights.
The Challenge
What Are Cool Down Logs and Why Do They Matter?
- Prevent Bacteria Growth: Cooling prepared foods quickly helps prevent bacteria growth in the "danger zone" temperature range.
- Manual vs. Automated Logs: Traditionally, cool down logs involve manual checks by kitchen staff over several hours, which can be labor-intensive and prone to error.
- Regulatory Compliance: Cool down logs are essential for regulatory compliance, preventing fines, health violations, and ensuring safety.
ConnectedFresh's Automated Cool Down Logs automate this process using IoT sensors to provide real-time data and alerts, eliminating manual checks. This not only saves time but ensures safety standards are met, giving operators peace of mind and allowing them to focus on quality dining experiences.
The process of logging cool-down sessions involves frequent checks – typically by kitchen staff – over several hours, which can be labor-intensive and is susceptible to human error. Maintaining accurate cool down logs is essential not just for food safety but also for regulatory compliance, as failing to cool food properly can lead to fines, health violations, or even foodborne illness outbreaks.
ConnectedFresh's Automated Cool Down Logs offer a solution that automates this critical process. By using IoT sensors, ConnectedFresh eliminates the need for manual checks, providing accurate, real-time data and automated alerts if the cooling process isn’t on track. This not only saves time but also ensures safety standards are consistently met, giving operators peace of mind and allowing them to focus on what matters most – providing high-quality dining experiences.
Maintaining consistency in food safety across dozens of locations is no small feat. Luna Grill faced challenges in manually logging the cooling process for prepared foods, which was labor-intensive and susceptible to human error. As they continued to expand, they needed a way to automate cooling logs to ensure compliance, minimize spoilage risk, and maintain the same high standard of quality at every Luna Grill location.
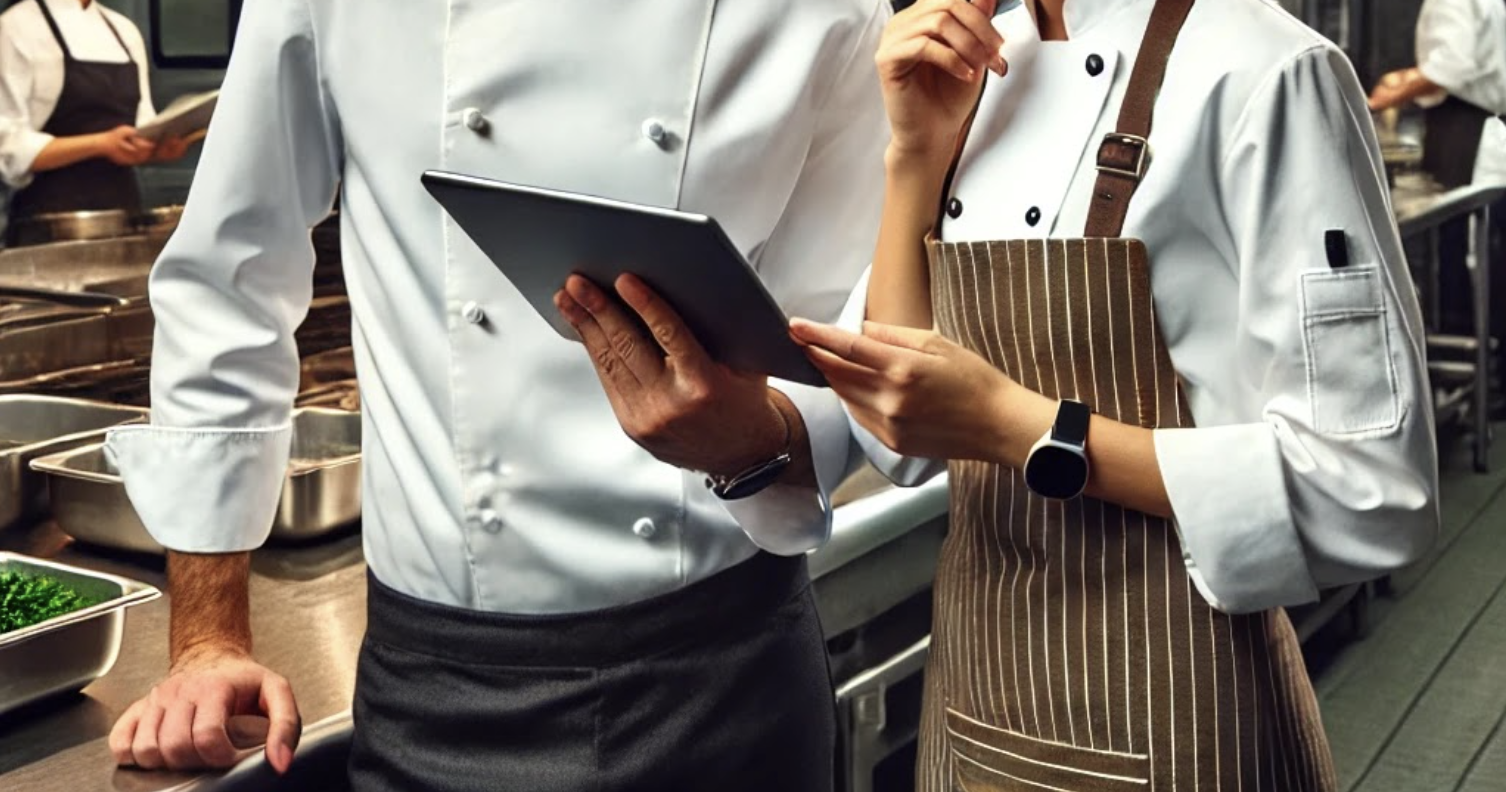
The Solution
- Automated Cool Down Logs Integration: ConnectedFresh introduced their Automated Cool Down Logs solution, seamlessly integrating IoT sensors with Luna Grill's refrigeration units in under two weeks, ensuring minimal operational disruption.
- Reduction in Manual Checks: Previously, staff monitored temperatures manually over a six-hour period to meet compliance. With ConnectedFresh, this task now takes less than five minutes, allowing team members to focus on customers.
- Ease of Implementation: The simplicity of ConnectedFresh's platform required minimal training, making the transition smooth and effective for Luna Grill’s staff.
Impact and Results
- Immediate Impact: Luna Grill immediately saw benefits after implementing ConnectedFresh's Automated Cool Down Logs. Proactive alerts enabled quick action to maintain safety standards.
- Prevented Issues: On several occasions, the temperature of cooling food wasn't dropping as expected, triggering alerts. The Luna Grill team adjusted procedures in real-time, preventing potential foodborne illness and ensuring compliance.
- Enhanced Cooling Efficiency: By implementing ConnectedFresh's Automated Cool Down Logs, Luna Grill cut down on the time required for monitoring cooled ingredients from an average of 20 minutes to less than 5 minutes. This efficiency saved thousands of hours across all locations.
- Labor Efficiency: Automating the cooling process saved each location significant time in labor - time that could instead be focused on other customer-centric tasks.
- Regulatory Compliance: The automated logging of cooling data made it easy for Luna Grill to stay ahead of regulatory audits, with detailed records available at the click of a button. Additionally, daily automated reports are sent to both store managers and leadership, ensuring ongoing compliance and proactive monitoring.
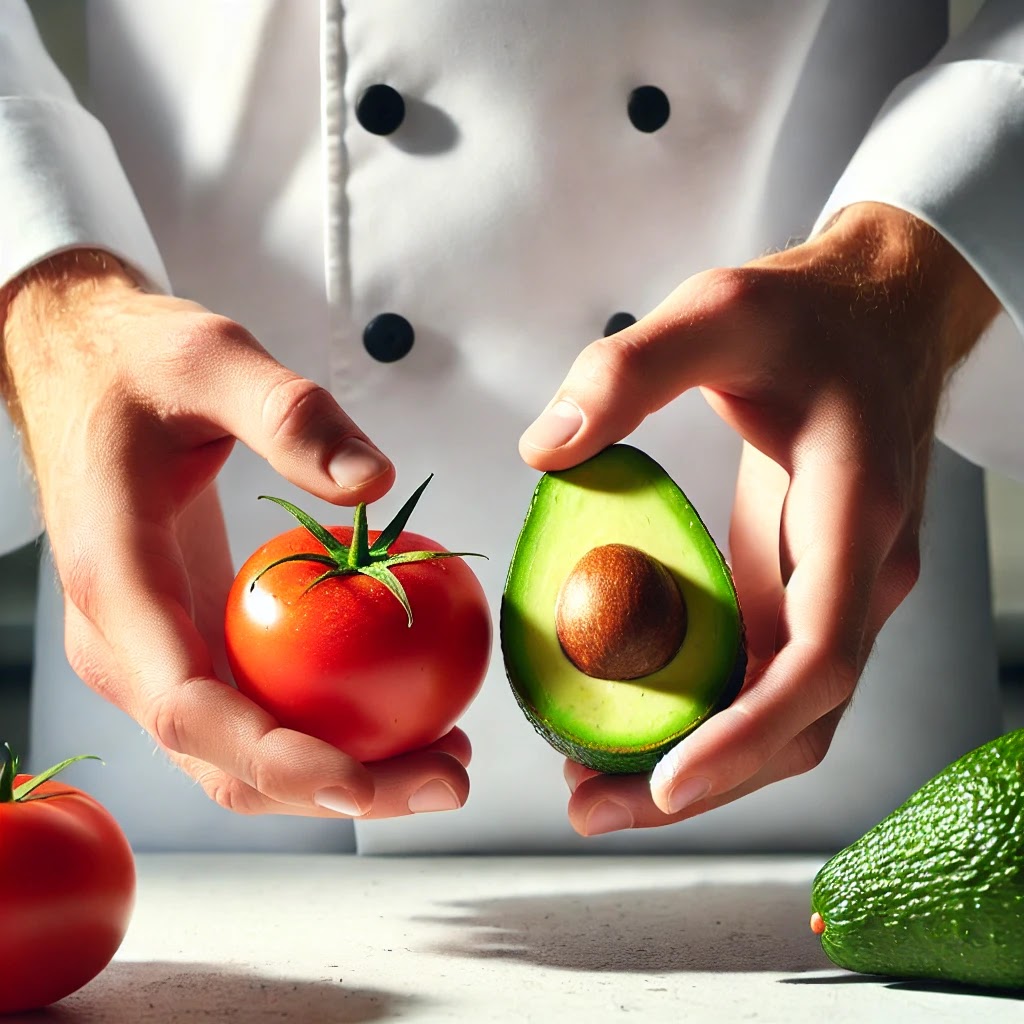
Peace of Mind
The food safety peace of mind is what really drove this project forward. Automated alerts and detailed reporting give us confidence that this critical control point is being handled with the utmost accuracy to meet health standards and regulations." - Maddie Ahrens, Director of Culinary & Restaurant Excellence at Luna Grill
Conclusion
For Luna Grill, partnering with ConnectedFresh meant more than just automating processes - it represented a commitment to quality, efficiency, and sustainability. By integrating automated cooling logs, Luna Grill has been able to grow with confidence, ensuring that every hummus bowl, kabob, and gyro served meets their standards for freshness and safety. ConnectedFresh's solutions have enabled Luna Grill to maintain operational excellence, reduce waste, and focus on what matters most: delivering delicious Mediterranean dishes to their loyal guests.
Ready to Automate Your Food Safety Processes?
Get started with ConnectedFresh today to streamline your operations, protect your food quality, and save thousands of hours in labor. Contact us now to learn how proactive monitoring can elevate your brand's commitment to safety and efficiency.
ConnectedFresh Perspective
The Automated Cool Down Logs solution is truly a game-changer. It's not just about compliance; it's about redefining how teams approach food safety with innovation. By automating and simplifying critical control points, we’re setting a new standard for efficiency and reliability in the industry. - Jake Simon, Co-founder of ConnectedFresh