$60,000 Saved in 3 Weeks: Grocery Warehouse Success with ConnectedFresh
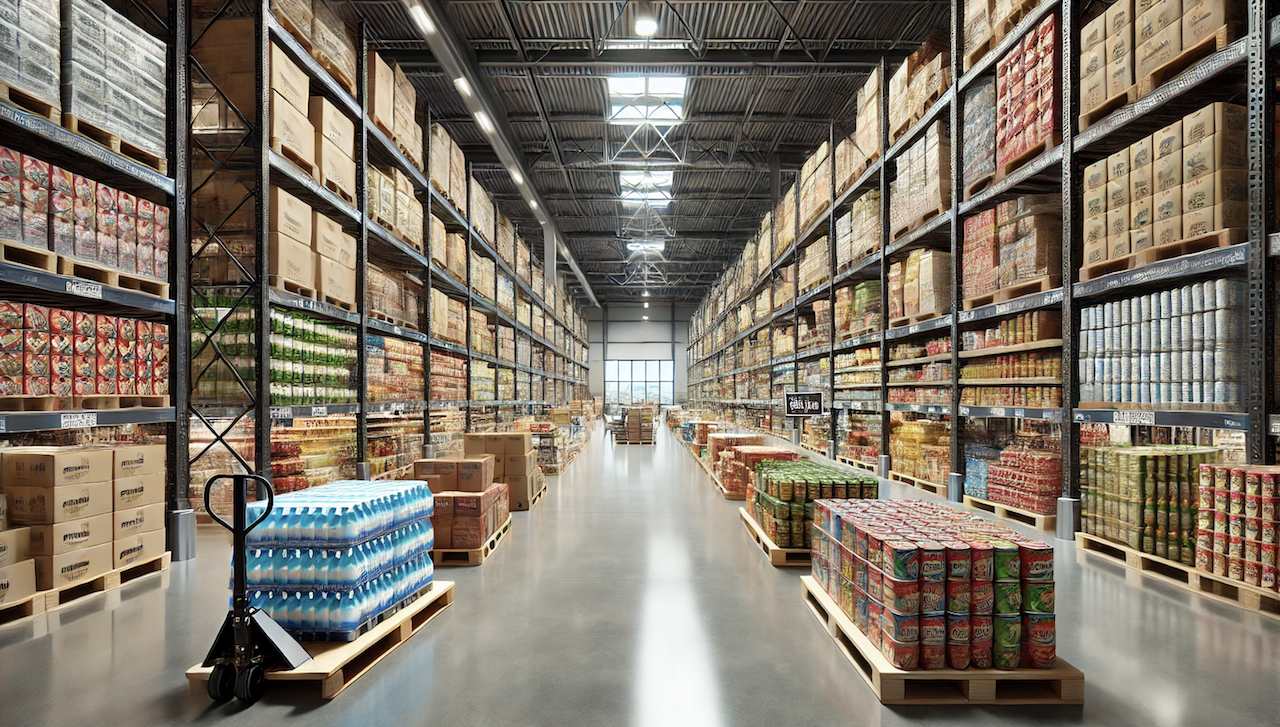
$60,000 Saved in 3 Weeks: Grocery Warehouse Success with ConnectedFresh
Within 3 weeks of implementing ConnectedFresh:
- $60,000 saved in potential product loss
- 32 labor hours saved
- Proactive monitoring led to immediate issue resolution
“The impact was immediate. Our team could make informed decisions in real-time, which saved us thousands of dollars in inventory. The ease of setup and the actionable alerts meant we were always a step ahead.” - Senior Manager of Operations, Grocery Warehouse Group
Overview
A major grocery warehouse group faced the challenge of maintaining optimal refrigeration temperatures to protect perishable goods. Across the food industry, ensuring consistent refrigeration is not just about maintaining product quality - it’s about complying with increasingly stringent food safety regulations and reducing food waste, both of which are crucial for sustainable operations. Within the first three weeks of setting up ConnectedFresh’s real-time monitoring solution, the warehouse group was able to avert potential product losses and save thousands of dollars.
The Challenge: Preventing Costly Product Losses & Ensuring Inventory Quality
Maintaining optimal refrigeration temperatures was a critical aspect of preserving product quality and avoiding costly spoilage. Equipment failures not only led to temperature spikes but also risked widespread inventory losses, increased waste, and operational disruptions. The grocery warehouse group needed a proactive, data-driven solution that would provide early warnings, allowing enough time to mitigate risks and protect their inventory effectively.
The Solution: Real-Time Monitoring with ConnectedFresh - Technical Insight & Seamless Integration
The grocery warehouse group implemented ConnectedFresh’s real-time monitoring solution across their locations, using a combination of reliable, off-the-shelf and proprietary IoT sensors that easily integrated with the warehouse's existing infrastructure. These sensors were selected for their proven accuracy in monitoring temperature, ensuring comprehensive coverage and compliance with food safety standards. The implementation was completed in under two weeks, minimizing disruption to day-to-day operations while seamlessly integrating into the warehouse’s existing infrastructure. By using the ConnectedFresh platform:
- Provided real-time alerts using IoT monitoring when temperature issues were detected, allowing staff to act quickly and prevent spoilage
- Enabled immediate action through proactive, data-driven insights to resolve issues quickly
- Offered customizable alerts, ensuring the team only received important notifications
Success Stories: Proactive Solutions to Prevent Major Losses & Drive Efficiency
Quick Action Saves $30,000 in Frozen Goods
- Early alert for temperature rise: A quick notification pointed to a temperature anomaly.
- Problem identified: A malfunctioning fan in the freezer.
- Outcome: Averted potential 50% product loss, saving an estimated $30,000.
- Labor saved: 16 hours spent in proactive issue resolution.
Early Alert Prevents $30,000 Loss in Perishable Inventory
- Temperature flagged in meat/dairy cooler: A ConnectedFresh alert signaled a problem with rising temperatures.
- Problem identified: A compressor failure.
- Outcome: Inventory was swiftly transferred to a reefer truck, preventing spoilage and saving $30,000.
- Labor saved: 16 hours dedicated to quick intervention.
Immediate Impact: Significant Savings Within Weeks
ConnectedFresh enabled the grocery warehouse group to take action within hours of detecting refrigeration issues, saving $60,000 in product loss and 32 labor hours - all within the first three weeks of implementation. The straightforward setup process, combined with customizable thresholds, delivered rapid results that extended beyond inventory savings, boosting employee efficiency and reducing emergency repair costs.
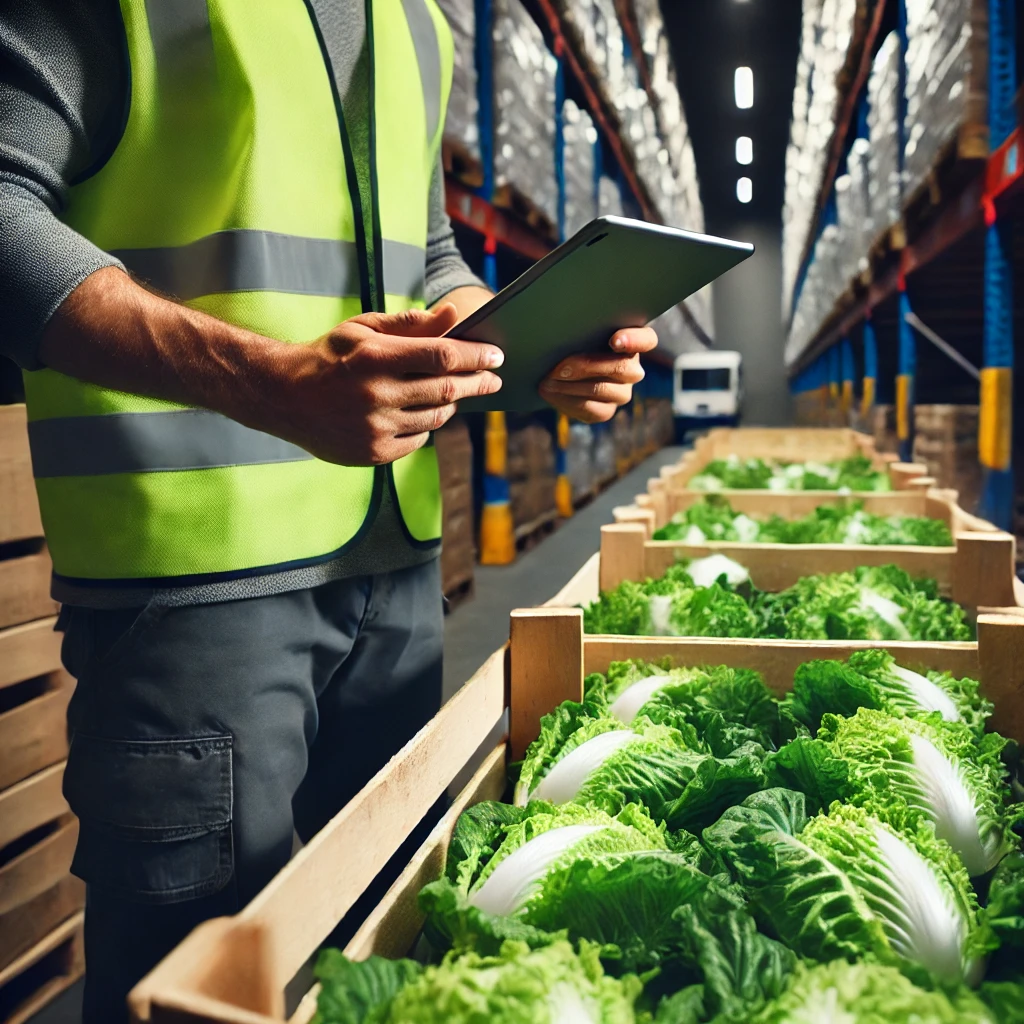
Why ConnectedFresh?
In today’s food industry, operational efficiency and food safety are key drivers of success. By aligning with these industry-wide goals, ConnectedFresh helps companies like grocery warehouse groups reduce waste, improve compliance, and ultimately enhance their reputation in the market.
Customizable Monitoring & Actionable Alerts The ConnectedFresh platform empowers the grocery warehouse group to:
- Quickly respond to equipment issues before they escalate
- Receive customizable thresholds and alerts that are highly actionable
- Optimize operations and prevent spoilage, ensuring inventory safety and operational efficiency
ConnectedFresh provided immediate value by delivering quick ROI, protecting inventory, and contributing to a broader industry effort to enhance food safety, reduce waste, and maintain compliance with regulatory requirements. By using best practices in IoT-driven smart monitoring, ConnectedFresh helps businesses comply with food safety regulations and positions them as leaders in sustainable, proactive inventory management. By offering tailored alerts and actionable insights, the system helped minimize alert fatigue, ensuring that every notification was relevant and needed.
“At ConnectedFresh, our goal is to protect inventory and streamline operations. When our client saved over $60,000 in three weeks, it confirmed for them that proactive monitoring is more than just a tool - it’s a game-changer for efficiency and savings.” - Jake Simon, Co-founder of ConnectedFresh
Ready to Protect Your Grocery Inventory?
Get started with ConnectedFresh today and take the first step towards reducing inventory losses, minimizing operational disruptions, and ensuring product quality. With seamless integration and proven results, there's no reason to wait. Contact us now to see how proactive monitoring can make an immediate impact on your bottom line.