Save Thousands Annually with Automated Cool Down Logs
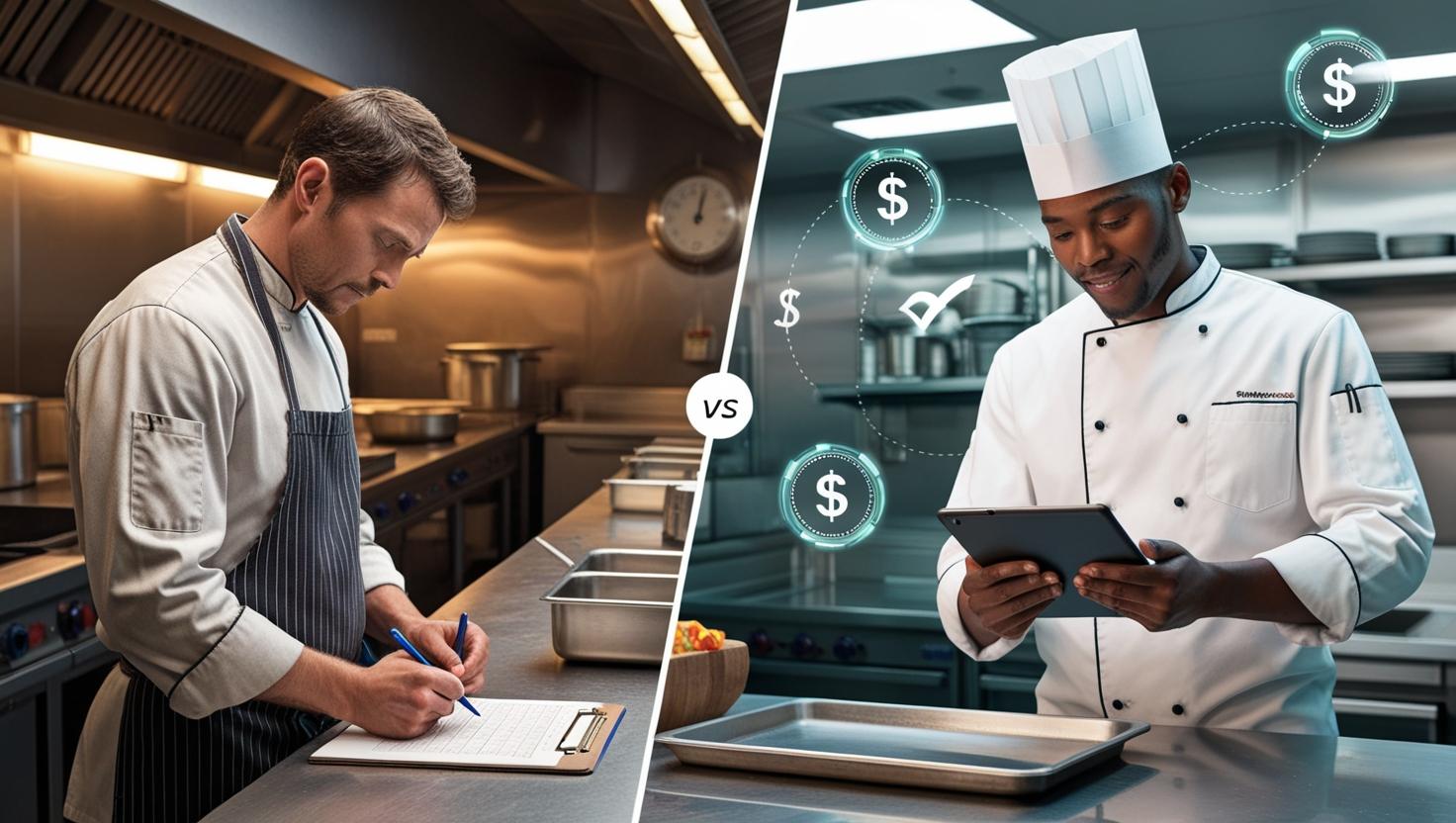
In today’s foodservice industry, every dollar counts. Rising costs of labor, energy, and food supplies - which have increased by over 10% in some regions over the past year - are driving businesses to optimize their operations and reduce waste.
For industries like restaurants, grocery chains, and foodservice operators, the cooling process for prepared foods presents a significant opportunity for savings. Automated cool down logs not only ensure compliance with food safety regulations but also provide a measurable financial impact by reducing labor costs, minimizing food waste, and preventing costly compliance violations. For smaller operators, this can mean saving hundreds of hours annually, while larger multi-unit brands may realize tens of thousands in combined savings through improved efficiency and reduced waste.
The Hidden Costs of Manual Cool Down Logs
Manually monitoring and logging the cooling process is more than just a time sink - it’s a source of hidden expenses:
- Labor Costs: Staff spend hours manually checking and recording temperatures, taking time away from other critical tasks.
- Human Error: Missed checks, incorrect recordings, or inconsistent practices can lead to food waste or compliance violations.
- Food Waste: Improperly cooled food must often be discarded, adding to unnecessary costs.
- Regulatory Fines: Non-compliance with food safety standards can result in fines, legal costs, or even temporary closures.
Automating Cool Down Logs: A Smart Investment
ConnectedFresh’s Automated Cool Down Logs eliminate the inefficiencies and risks associated with manual processes, offering a high return on investment. Here’s how automation translates to savings:
1. Reduced Labor Costs
Manual cool down logging requires staff to spend hours over a six-hour cooling window, checking temperatures every 15-30 minutes. With automation, this process is reduced to less than 5 minutes of active time, saving hundreds of labor hours annually. For example, a multi-unit operator logging five cooling sessions daily can save thousands of dollars in labor costs each year.
2. Minimized Food Waste
Real-time monitoring and alerts ensure that cooling issues are addressed immediately. By acting quickly, operators can prevent spoilage and reduce waste. For instance, addressing a cooling issue promptly in a high-value cooler can save $5,000 to $15,000 in food during a single incident, depending on the inventory involved and the scale of the operation. These savings multiply significantly over time for multi-unit operations.
3. Avoidance of Compliance Violations
Automated logs provide a verifiable record of compliance, reducing the risk of fines or legal repercussions. During audits or inspections, operators can confidently present detailed, accurate records that meet regulatory standards.
4. Operational Efficiency
Automation frees staff to focus on customer service or other operational priorities, improving overall productivity. The ripple effect of improved efficiency can translate into better service and higher customer satisfaction.
Real-World Example: Scaling Savings Across Multiple Locations
Consider a multi-unit restaurant operator managing 20 locations. If each location logs five cooling sessions daily, manual logging could consume 1,500 labor hours annually across all units. For larger operations, with 50 or 100 locations, this time and cost multiplies exponentially, potentially saving tens of thousands in labor costs annually with automation. By automating this process with ConnectedFresh, the operator could save:
- 1,350 labor hours annually (90% reduction)
- $20,000-$30,000 in labor costs
- Thousands more in avoided food waste and compliance risks
The scalability of these savings makes automation an essential investment for growing brands.
The Bigger Picture: Why Automation Matters
Automated cool down logs are more than just a compliance tool - they’re a strategic advantage.
- Scalability: Whether you operate a few locations or hundreds, automation provides consistent, reliable processes.
- Actionable Insights: Real-time data helps identify trends, allowing operators to proactively address recurring issues.
- Peace of Mind: Knowing that food safety processes are automated ensures confidence for both operators and customers.
Take the Next Step Toward Savings
Ready to save thousands annually while improving compliance and efficiency? Schedule a demo today to see how ConnectedFresh’s Automated Cool Down Logs can transform your operations. Let’s optimize your processes, protect your inventory, and give your team the tools they need to thrive.