The ConnectedFresh Advantage: Redefining Food Safety with IoT
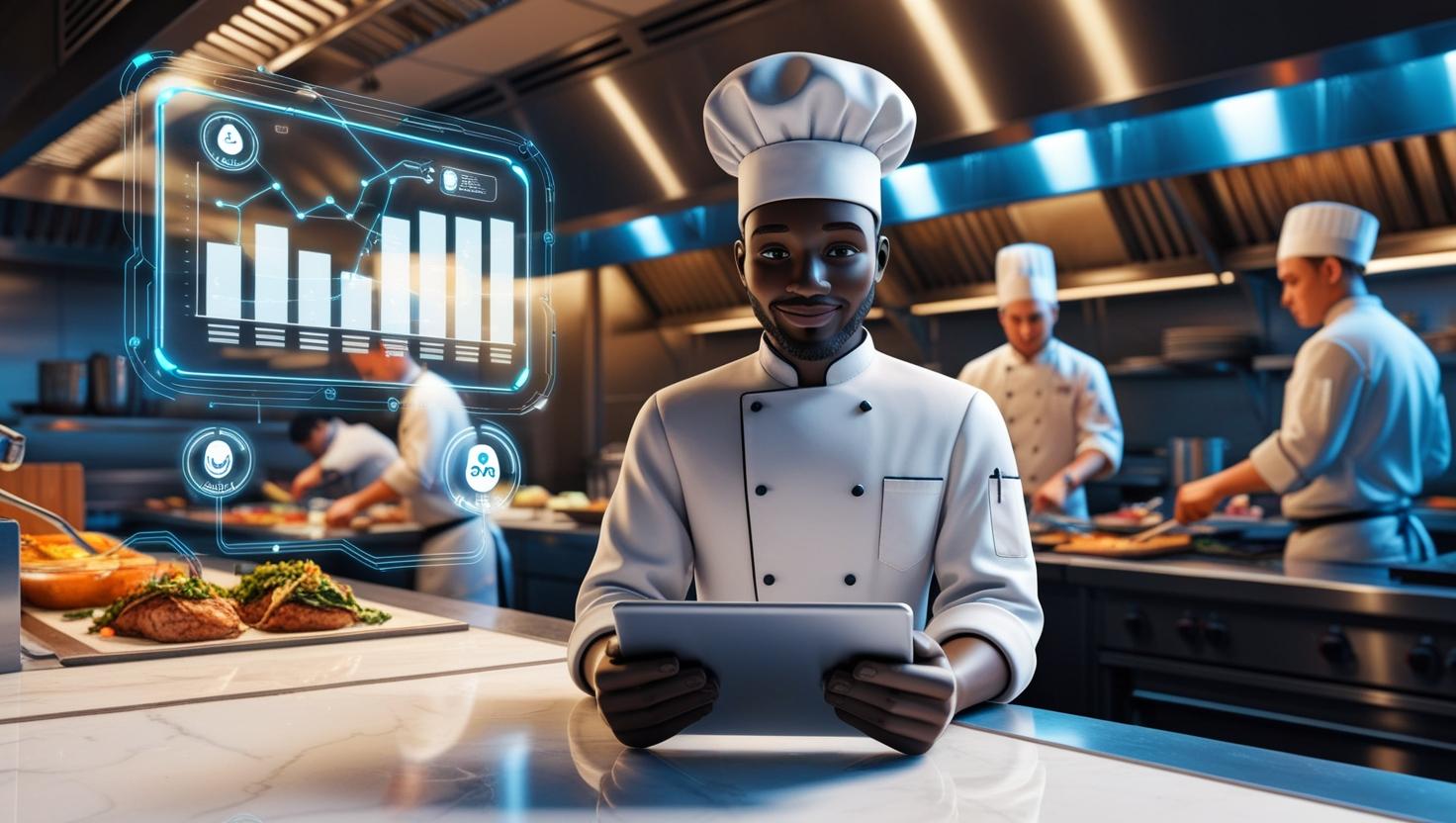
In today’s fast-paced foodservice industry, traditional monitoring tools are no longer sufficient to meet the growing challenges of compliance, operational efficiency, and waste reduction. ConnectedFresh is at the forefront of food safety innovation, offering a transformative approach to monitoring and operational insights. Unlike conventional solutions, ConnectedFresh combines advanced IoT technology with actionable analytics, empowering businesses to take proactive control of their operations. For example, a restaurant operator used ConnectedFresh to identify irregular cooling patterns in a walk-in freezer, preventing a $10,000 inventory loss through timely intervention. By not manufacturing sensors, ConnectedFresh has the flexibility to choose the best off-the-shelf hardware to meet diverse needs, including water flow, air quality, fill levels, and more.
Why Food Safety Requires a Smarter Approach
Food safety is non-negotiable, but ensuring it across multiple locations is complex and labor-intensive. Traditional methods, such as manual temperature checks and basic data loggers, often leave operators reactive instead of proactive. This approach leads to:
- Missed Issues: Subtle anomalies in equipment performance can go unnoticed until it’s too late, resulting in costly food waste or compliance violations.
- Labor-Intensive Processes: Staff time is consumed by manual checks and logging, diverting attention from customer-facing tasks.
- Limited Insights: Basic monitoring tools provide raw data but no actionable insights to guide decision-making.
How ConnectedFresh Stands Out
ConnectedFresh goes beyond monitoring to provide real-time insights that prevent problems before they occur. Here’s what sets us apart:
1. Predictive Analytics for Proactive Action
Our IoT sensors analyze trends to detect anomalies before they become critical. ConnectedFresh leverages machine learning and historical data to identify subtle shifts in equipment performance, such as cooling inefficiencies or irregular energy consumption, setting it apart from competitors that rely solely on high/low thresholds. Whether it’s a cooler showing early signs of compressor failure or a door left ajar, ConnectedFresh alerts teams in real-time, enabling immediate intervention with actionable insights.
2. Tailored Alerts That Drive Action
ConnectedFresh offers intelligent, customizable thresholds and notifications tailored to your operations, analyzing patterns and anomalies to ensure precision and reduce unnecessary alerts. For example, a grocery chain used ConnectedFresh’s intelligent alerts to detect a freezer door left ajar during overnight hours. The system’s immediate notification, based on detecting an irregular cooling pattern, allowed staff to act quickly, preventing spoilage and saving thousands of dollars. This minimizes alert fatigue and ensures that your team focuses on actionable priorities.
3. Seamless Integration with Existing Systems
ConnectedFresh’s platform integrates effortlessly with compliance tools, facilities management systems, and more. The flexibility of integrating various off-the-shelf sensors ensures adaptability for unique operational needs, such as leak detection or energy monitoring. For example, our data can automatically trigger a maintenance request in Ecotrak or initiate corrective actions in CMX1, turning insights into action without manual intervention.
4. Scalable Solutions for Multi-Unit Brands
Whether you operate five locations or 500, ConnectedFresh provides consistent, reliable monitoring across all units. By not being tied to proprietary hardware, our platform ensures scalability and customization to meet the unique needs of operations at any size. Our platform scales seamlessly, offering unified insights for executives while empowering local teams with the data they need.
Real-World Impact: Success Stories
Saving Thousands for Grocery Warehouses
By using ConnectedFresh to monitor their refrigeration units, a major grocery warehouse group leveraged predictive analytics to act on early warnings of cooling failures. Within three weeks, they:
- Saved $60,000 in potential product loss.
- Reduced labor hours by 32, freeing up staff for other priorities, such as customer service and operational efficiency.
Efficiency Gains at Luna Grill
Luna Grill automated their cooling logs across 50+ locations with ConnectedFresh. The results:
- 75% reduction in logging time per cooling session.
- Thousands of labor hours saved annually.
- Enhanced compliance with health regulations by automating reporting and simplifying audits. ConnectedFresh’s digital logs and real-time monitoring ensure accurate records are always available for health inspections, reducing the burden on staff and minimizing the risk of compliance violations.
The Bigger Picture: Empowering Foodservice Operators
ConnectedFresh’s mission is to empower foodservice operators with the tools they need to protect inventory, improve efficiency, and ensure compliance. By leveraging advanced IoT technology, predictive analytics, and seamless integration capabilities, we deliver tailored solutions that address the unique challenges of modern foodservice operations while enabling proactive and sustainable practices. By focusing on actionable insights and seamless integration, we help businesses stay ahead in an increasingly complex landscape.
Take the Next Step
Ready to transform your food safety operations? Schedule a demo today to see how ConnectedFresh can deliver real results for your business. Let’s redefine what’s possible in food safety together.