The Hidden Costs of Food Safety Compliance: Why Automation is Essential
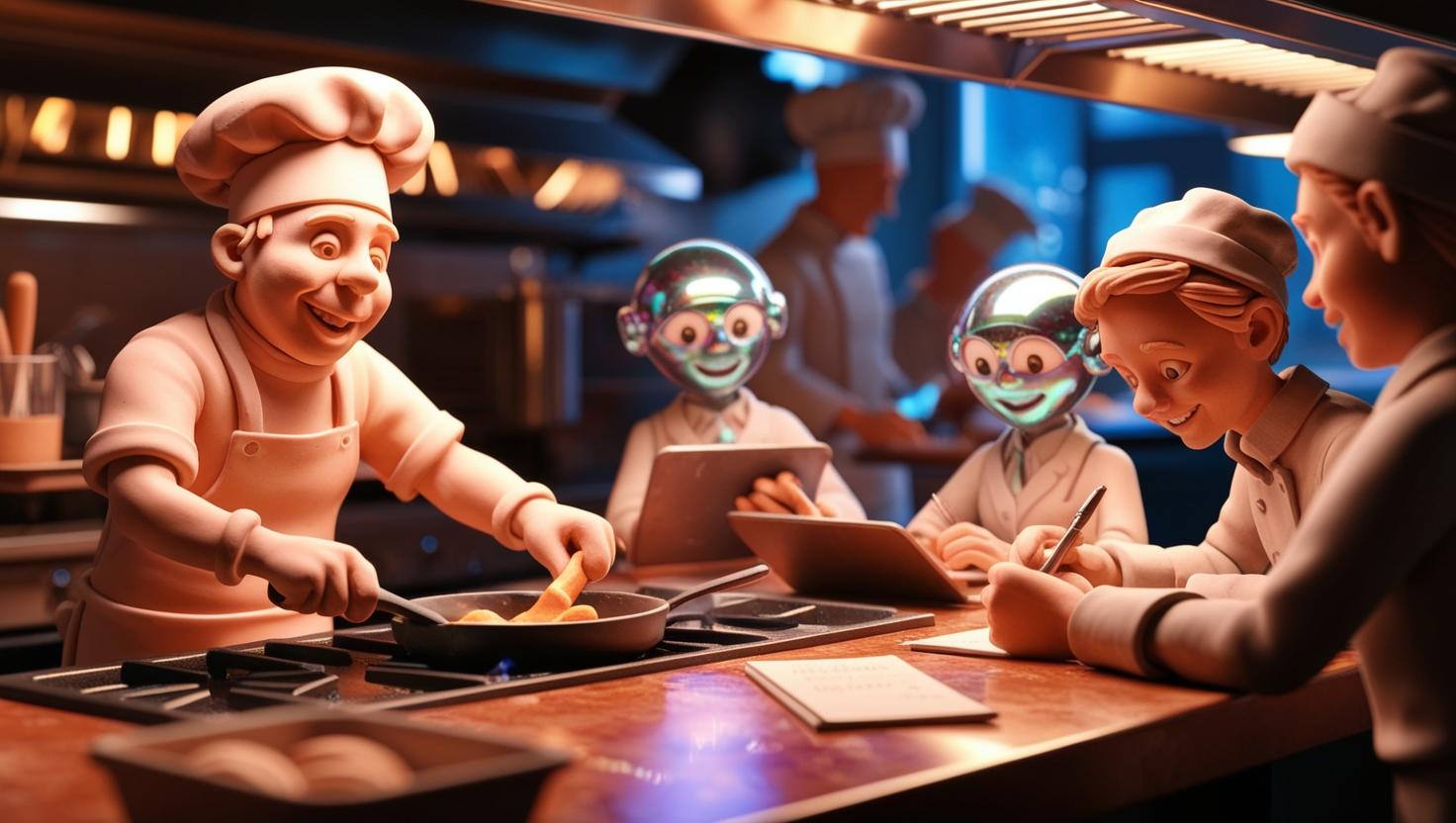
In the fast-paced world of foodservice, compliance with food safety regulations is non-negotiable. However, many businesses underestimate the operational and financial toll of managing these processes manually. From labor-intensive logs to missed compliance deadlines, the hidden costs add up quickly - and they’re impacting your bottom line more than you think.
The Problem: The True Costs of Manual Processes
1. Labor Costs and Time Inefficiencies
Manual food safety tasks, such as cool down logs or temperature monitoring, often require staff to step away from customer-facing responsibilities. Each manual task adds up:
- Time Spent: Checking temperatures and logging data can take 20+ minutes per item, multiple times per day. Across dozens of units, this can result in thousands of labor hours annually.
- Staff Turnover Impact: High turnover in foodservice means constant retraining on labor-intensive processes, further straining resources.
2. Human Error and Compliance Risks
Manual processes are inherently prone to mistakes, whether from missed entries, inaccurate data, or inconsistent recordkeeping. This can lead to:
- Regulatory non-compliance, fines, or failed audits.
- Health risks due to improperly handled food.
3. Financial Losses from Reactive Problem-Solving
When an issue arises - like a cooler failing - manual processes often mean operators are reacting after the damage is done. Spoiled inventory and emergency repairs cost thousands, and reputational damage can be even harder to recover from.
The Solution: Automation to the Rescue
Automation removes the guesswork and inefficiencies of manual processes, offering a streamlined, scalable way to ensure compliance, protect your inventory, and save costs.
How ConnectedFresh Solves These Challenges
1. Real-Time Monitoring and Alerts
ConnectedFresh uses IoT-driven sensors to continuously monitor critical metrics like food temperatures. When an issue arises, automated alerts notify staff immediately, allowing for proactive solutions before problems escalate.
2. Labor Savings
Automating tasks like cool down logs eliminates the need for staff to spend hours manually checking and recording temperatures. With ConnectedFresh, processes that once took 20 minutes now take less than 5 minutes, saving thousands of hours across locations.
3. Enhanced Accuracy and Compliance
Digital logs generated automatically by ConnectedFresh ensure consistent, error-free records that meet FDA and health department standards. This simplifies audits and gives operators peace of mind.
4. Data-Driven Insights
ConnectedFresh doesn’t just log data; it provides actionable insights. For example:
- Identify recurring cooling issues in specific units, enabling preventive maintenance.
- Spot trends across locations to optimize operations.
Why This Matters for Foodservice Operators
Whether you operate a small multi-unit group or a nationwide chain, automation scales with your needs. Key benefits include:
- Cost Savings: Reduce labor costs and minimize spoilage with real-time monitoring.
- Operational Efficiency: Free up staff to focus on customer experience instead of tedious manual tasks.
- Compliance Confidence: Ensure consistent adherence to food safety standards across all locations.
- Reputation Protection: Proactively address issues to prevent health risks and maintain customer trust.
Real-World Example: Luna Grill’s Transformation
One of ConnectedFresh’s clients, Luna Grill, eliminated manual cool down logs across their 50+ locations. By automating this critical process, they achieved:
- A 75% reduction in logging time, saving thousands of labor hours annually.
- Real-time alerts that allowed teams to act quickly, preventing compliance risks.
- Enhanced peace of mind, knowing their cooling processes were consistent and safe.
Conclusion: The Future of Food Safety is Automated
Manual processes no longer cut it in today’s competitive foodservice landscape. The hidden costs - in labor, compliance risks, and financial losses - are simply too high. By automating food safety compliance with solutions like ConnectedFresh, operators can ensure their teams stay efficient, compliant, and focused on delivering exceptional food experiences.
Ready to Automate?
Let ConnectedFresh help you eliminate the hidden costs of manual compliance. Schedule a free consultation to learn how automation can revolutionize your operations and protect your bottom line.