Why Food Safety Demands More Than Basic Monitoring
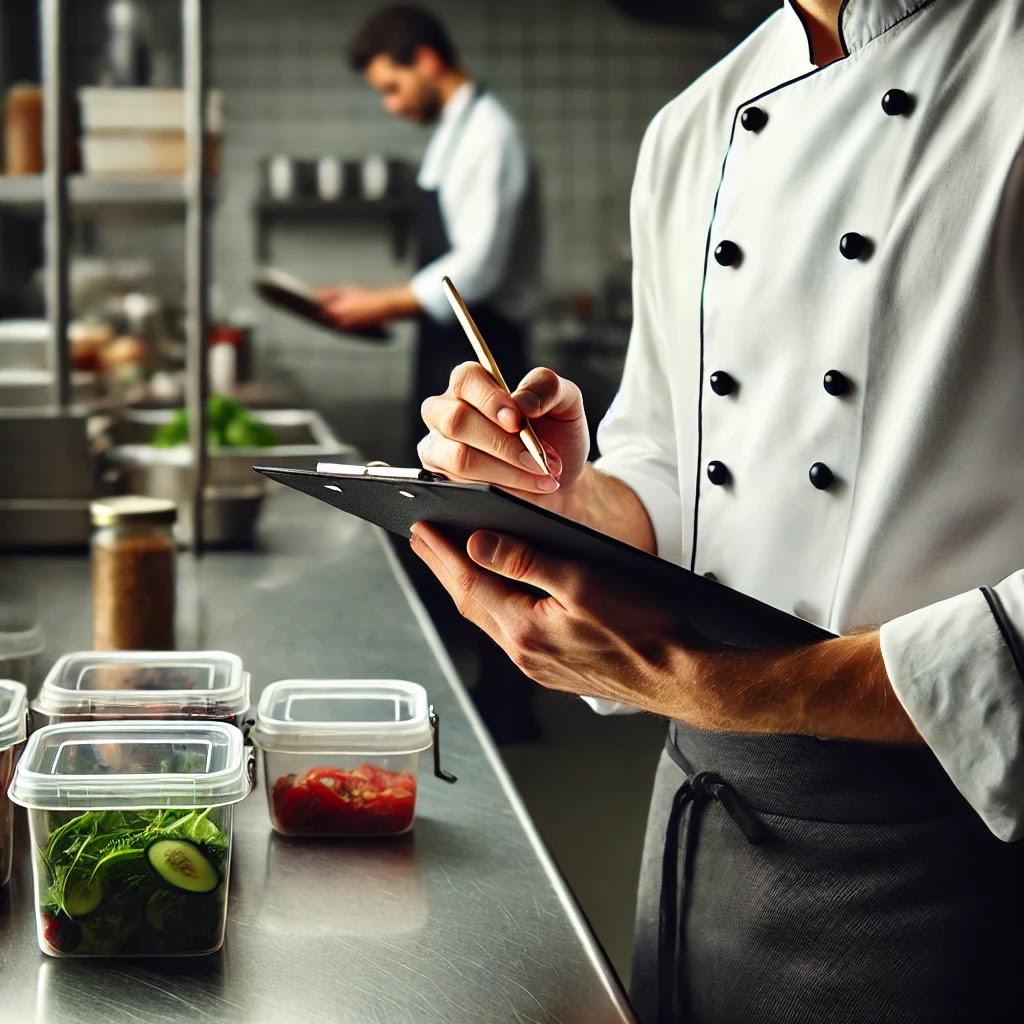
For foodservice operators, maintaining food safety is non-negotiable. Yet, relying on basic monitoring tools, such as simple temperature logs, can leave businesses exposed to risks ranging from spoilage to compliance violations. As the industry grows more complex and regulated, operators must embrace solutions that go beyond monitoring to deliver actionable insights and proactive interventions.
The Limitations of Basic Monitoring
Basic monitoring tools, such as manual temperature checks or standalone data loggers, provide foundational information, but they fall short in key areas:
- Reactive Nature: They detect issues only after they’ve escalated, leading to wasted inventory or safety concerns.
- Data Overload Without Insights: These tools capture raw data but lack the analytics to identify trends or predict failures.
- Labor-Intensive Processes: Manual checks and paper logs consume time, leaving staff less available for customer-focused tasks.
The Need for Advanced Solutions
Modern food safety demands proactive and scalable solutions that address the challenges of today’s fast-paced foodservice environments. ConnectedFresh’s platform exemplifies this next generation of monitoring by:
1. Turning Data Into Insights
Instead of providing raw numbers, ConnectedFresh transforms data into actionable insights. For example:
- Alerts identify temperature anomalies before they become critical.
- Pattern recognition predicts when equipment might fail, allowing teams to act in advance.
2. Automating Labor-Intensive Processes
By automating processes like temperature logging and compliance reporting, ConnectedFresh saves time while improving accuracy. Staff are freed up to focus on high-value tasks, enhancing both operational efficiency and customer experience. Additionally, the intuitive nature of ConnectedFresh minimizes training demands, ensuring smooth adoption even with high staff turnover.
3. Customizable and Scalable Solutions
ConnectedFresh’s flexibility allows operators to monitor a variety of metrics beyond temperature, breaking down data silos and streamlining information flow across systems, including:
- Door status to ensure proper equipment usage.
- Water flow and quality to prevent costly leaks or contamination.
- Energy consumption to identify inefficiencies and reduce costs.
- Fill levels for waste bins to optimize collection schedules and avoid overage fees.
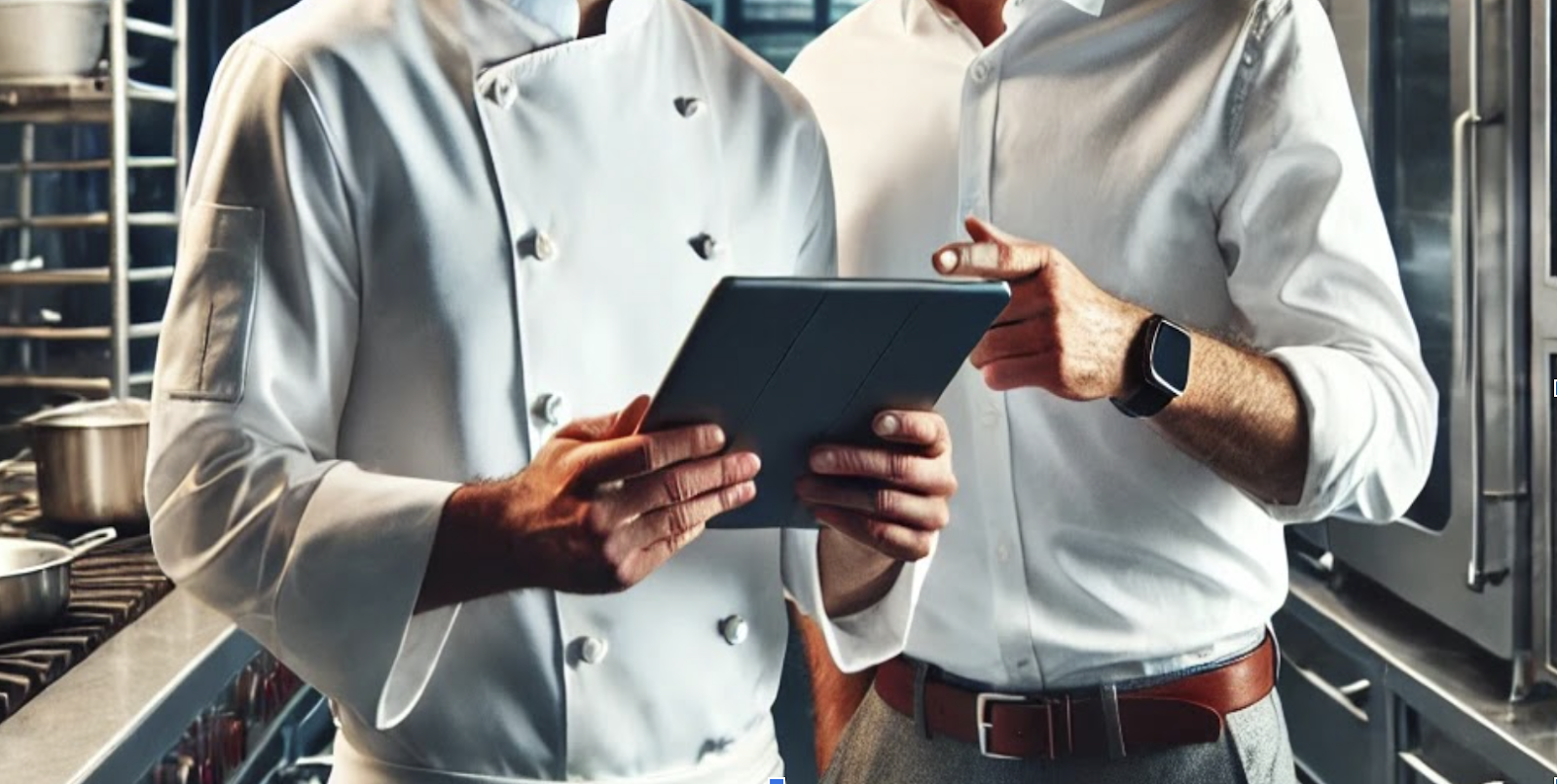
Why Staying Proactive Matters
The cost of reactive management goes beyond wasted inventory. Delays in addressing food safety issues can lead to:
- Compliance Fines: Health inspections often require detailed logs and immediate actions, which reactive systems may not support.
- Reputational Damage: Customers expect consistent quality, and safety lapses can undermine trust.
- Operational Disruptions: Emergency repairs or inventory losses disrupt workflows and strain budgets.
Proactive systems like ConnectedFresh mitigate these risks by ensuring operators are always one step ahead. This scalability makes it easy to adapt from single-unit operators to multi-location enterprises, delivering consistent and reliable performance at every level.
Real-World Impact: Success Stories
Grocery Chain Saves $60,000 in Product Loss
A major grocery chain used ConnectedFresh’s predictive analytics to detect cooling inefficiencies in a freezer. Acting quickly, they avoided a complete breakdown, saving $60,000 in inventory and significant labor hours.
Luna Grill Cuts Logging Time by 75%
By automating cooling logs across 50+ locations, Luna Grill achieved a 75% reduction in time spent on temperature checks, allowing staff to focus on customer service and operational improvements.
Quick-Service Restaurant Optimizes Waste Management
Using ConnectedFresh to monitor dumpster fill levels, a quick-service restaurant reduced overage charges by 30% while improving collection efficiency.
The ConnectedFresh Advantage
Unlike basic monitoring tools, ConnectedFresh provides a comprehensive solution tailored to the unique challenges of foodservice operations. Key benefits include:
- Real-Time Alerts: Immediate notifications allow operators to address issues proactively, minimizing downtime and preventing costly losses.
- Comprehensive Metrics: Monitor beyond temperature, from water quality to energy usage, offering unmatched operational visibility.
- Seamless Integration: Easily connects with compliance systems, facilities management tools, and communication platforms like Slack or Teams, delivering critical insights wherever they’re needed.
- Scalability: Designed to grow with your business, ConnectedFresh supports operations from small businesses to enterprise-level multi-unit brands.
"ConnectedFresh's proactive alerts and seamless integration have revolutionized how we manage food safety and efficiency. The platform is intuitive and has saved us both time and significant costs." - Director of Operations, Multi-Unit Restaurant Group
Ready to Move Beyond Basic Monitoring?
ConnectedFresh is here to help you elevate your food safety strategy with actionable insights and proactive solutions. Schedule a demo today to discover how our advanced platform can revolutionize your operations and protect your bottom line.